PDC (Product Design Change)
Best Product Design Change Management software, provides a structured approach to managing design changes
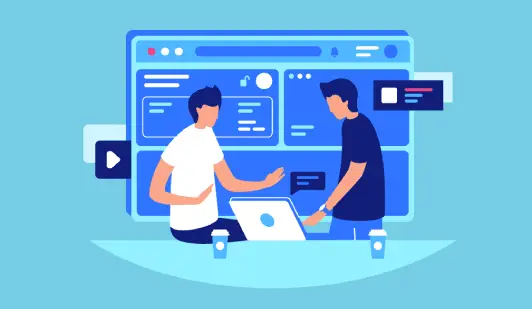
Empowering businesses with world-class custom software development solutions
Best Product Design Change Management Software
In today’s fast-paced industrial landscape, efficiently managing product design changes is critical for quality and compliance. Our Product Design Change Management Software streamlines the lifecycle of design change requests— from initiation to closure— ensuring systematic capture, review, and execution of modifications driven by innovation or compliance.
The software offers role-based access, detailed tracking, and automated notifications to ensure timely communication across all departments involved.
Cross-functional teams (CFT) such as R&D, Production, Quality, Supply Chain, and Marketing can collaborate seamlessly, maintaining full visibility on change impacts, dependencies, and approvals. Every step is time-stamped and logged to create a digital audit trail that aligns with ISO and regulatory compliance standards.
Our Design Change module is customizable to fit your organizational workflows, allowing for flexible configurations, multiple approval hierarchies, and integration with your existing ERP or PLM systems. It helps remove miscommunication, manual errors, and unnecessary delays while promoting informed decision-making.
Whether you’re working in FMCG, Automotive, Electronics, or Pharma, this tool helps ensure that every product design change module is implemented with clarity, control, and confidence.
Key Benefits
Best Product Design Change Management Software
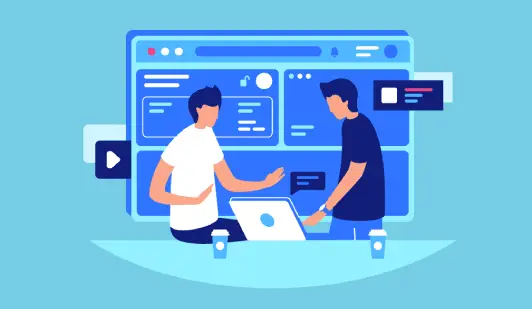
Design Change Workflow
Change Request Initiation
Any stakeholder (e.g., QA, R&D, Production) can initiate a design change request with reason, impact analysis, and supporting documents.
Impact Assessment & CFT Review
Cross-functional teams assess the change for its impact on product performance, packaging, compliance, supply chain, and customer satisfaction.
Approval Hierarchy
The request goes through multiple levels of approval (e.g., QA Head, Plant Head, R&D Head, BU Head) as per defined configuration.
Implementation Plan
Post-approval, tasks are assigned to relevant departments for tool modification, artwork changes, machine setup, or BOM updates.
Validation & Closure
After successful implementation, final verification and closure are done. The system archives the full record for future reference.
Why Choose Havteq’s
Best Product Design Change Management Software?
Industry-Specific Expertise
We understand the complex challenges of manufacturing, FMCG, pharma, and engineering sectors—our solutions are designed to match real-world operational needs.
Seamless Integration
Whether it’s SAP, Oracle, or your custom ERP/PLM—our solution integrates smoothly with your existing tech stack.
Configurable to Your Business
Our software isn't one-size-fits-all. We offer customizable workflows, fields, forms, and user roles tailored to your organizational structure.
Advanced Reporting & Insights
Get real-time dashboards, KPIs, and audit trails for faster decision-making and continuous improvement.
Data Security & Compliance
Our platform is developed with ISO 27001 standards in mind and supports regulatory compliance like 21 CFR Part 11, ISO 9001, and more.
Trusted by Industry Leaders
Our clients include leading enterprises that rely on our platform for process automation, compliance, and operational excellence.
Quick Implementation & Training
With guided onboarding, user-friendly design, and responsive support, your teams can go live in weeks—not months.
Frequently Asked Questions
Know more about Product Design Change Software
Can the software be customized to match our internal approval flow?
Yes, the workflow engine is highly flexible and allows configuration of multi-stage approvals, role-based routing, and conditional logic.
Does it integrate with ERP or PLM systems?
Absolutely. The software supports integration with popular ERP and PLM systems to ensure consistency in part numbers, BOM, and production planning.
Can it Deal multiple types of design changes?
Yes, it supports changes related to mechanical parts, packaging, labeling, raw materials, and electronic components—all with customizable forms.
Is it compliant with ISO and FDA regulations?
Yes, the software maintains detailed logs, audit trails, and version control to comply with ISO 9001, ISO 13485, and 21 CFR Part 11 guidelines.
Is it available on desktop or cloud?
Our solution is available both as an on-premise desktop application and a secure cloud-based platform, depending on your organization’s needs.
Is the software aligned with Lean or ISO practices?
Yes, the platform is built to support Lean practices, 5S, and ISO management systems by enabling real-time documentation, traceability and closure tracking.